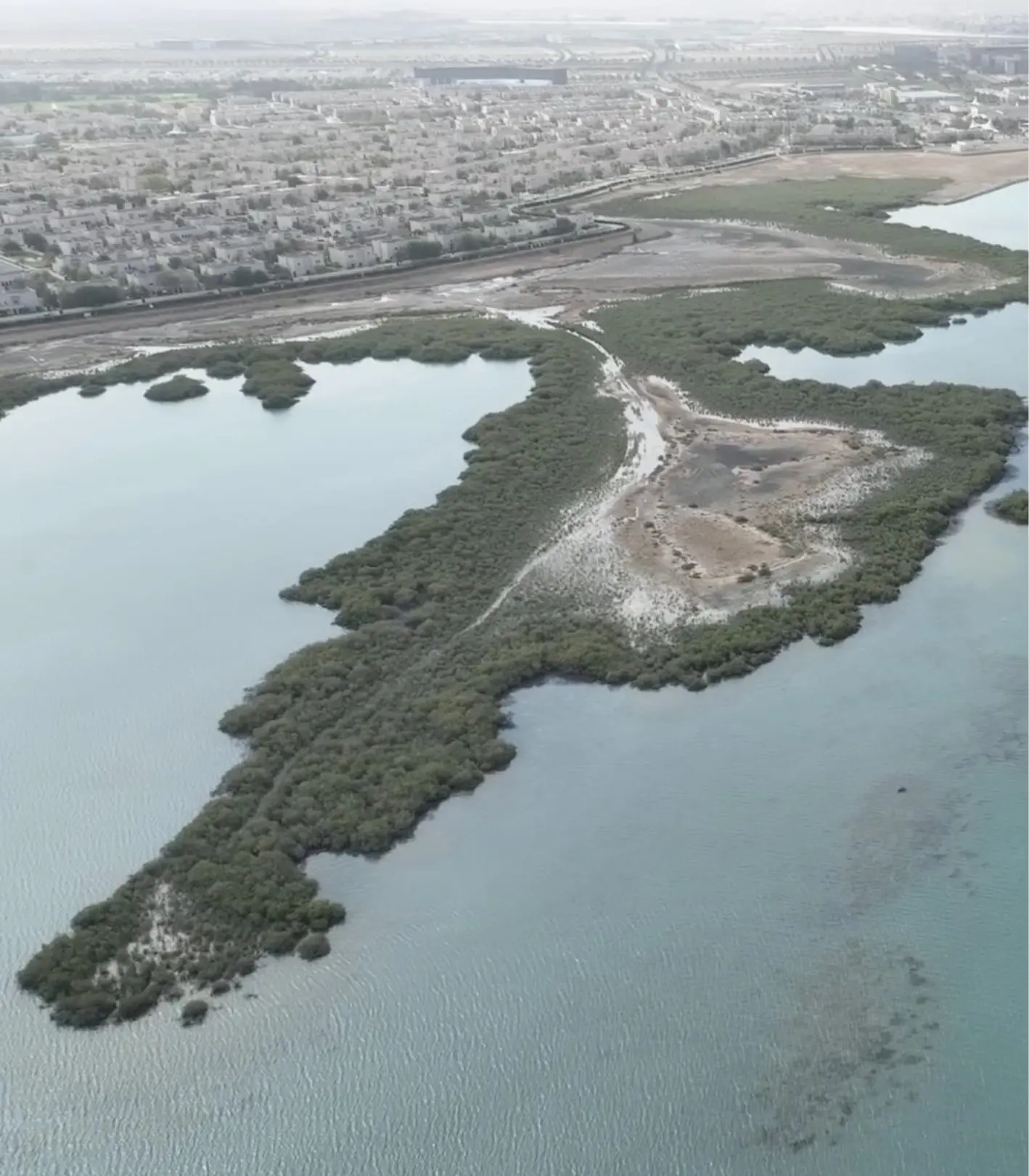
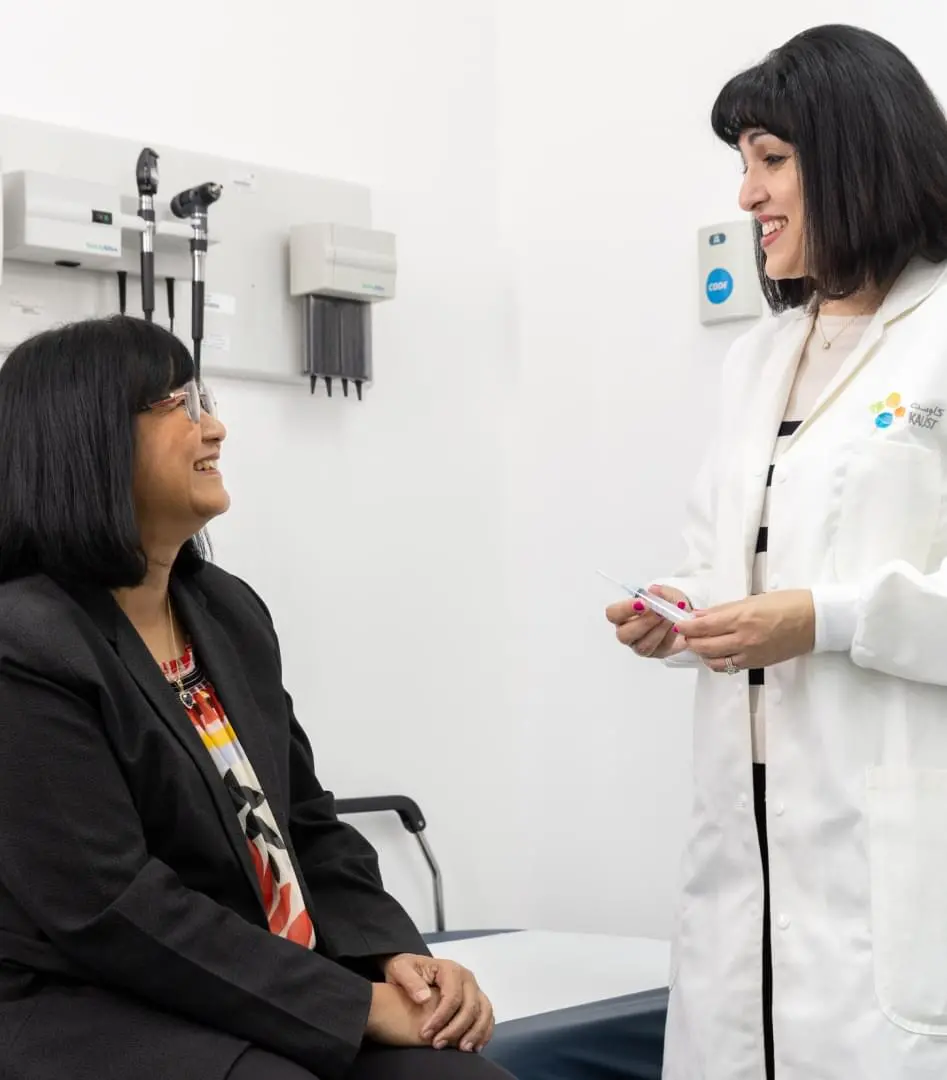
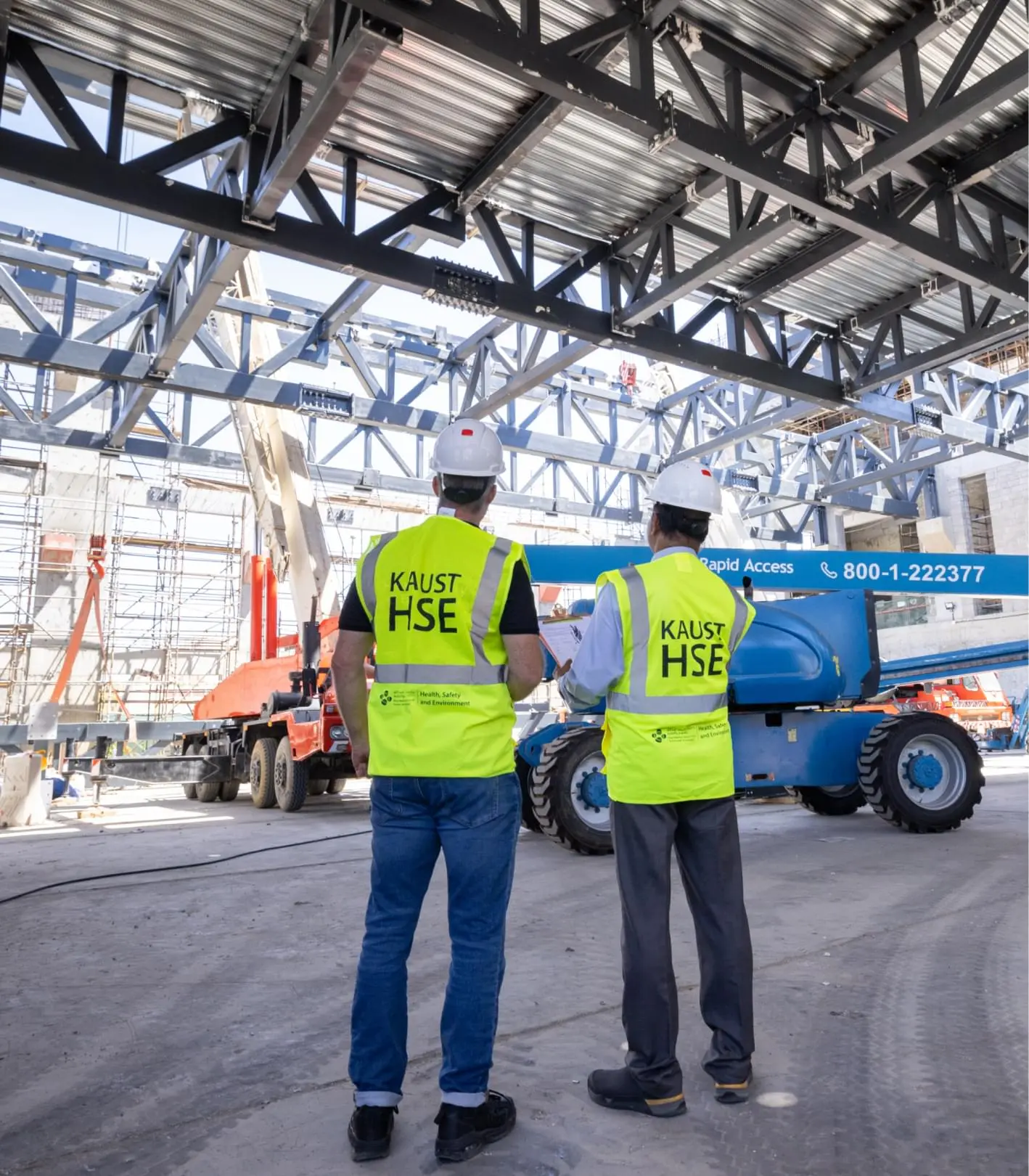
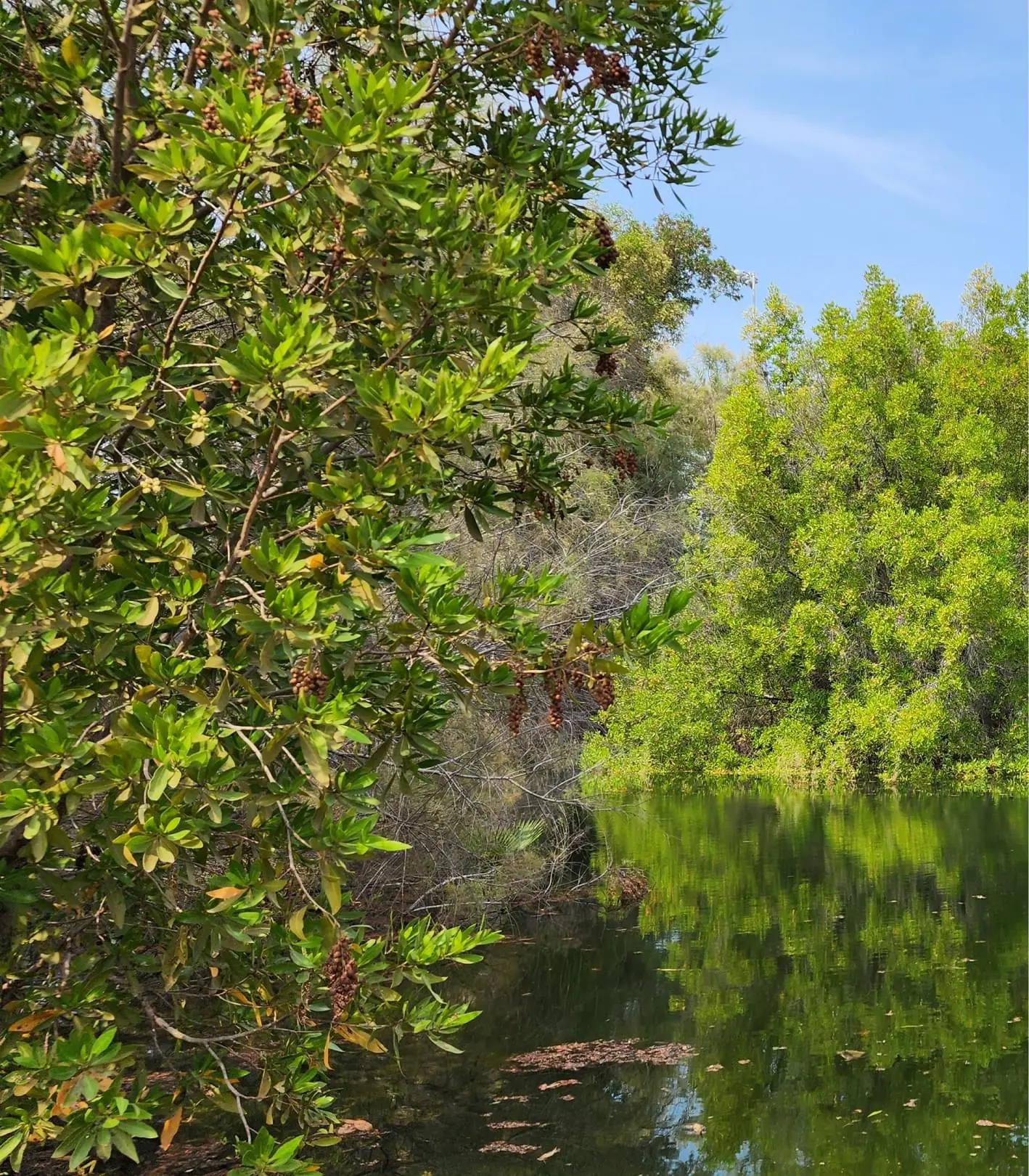
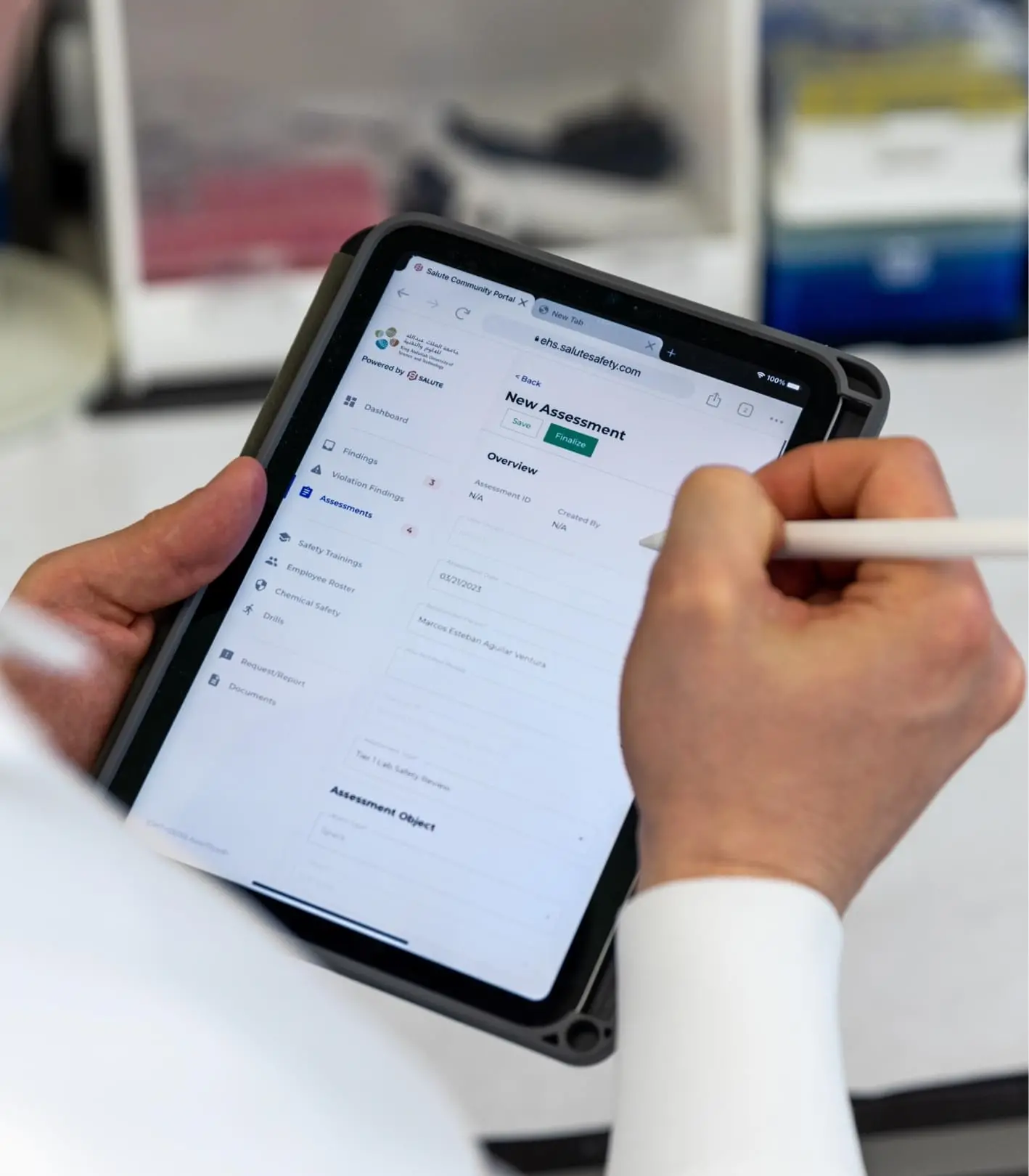
Quick Links:
In KAUST there are several, state-of-the-art, machinery and mechanical tools workshops for serving the researchers in their prototyping and fabrication projects. All of these workshop spaces, machines, and tools arecontrolled and managed by the “The Prototyping and Product Development Core Lab”.
The Reverse Engineering Lab (REL) provides dimensional, analytical and electrical quality inspections, and is equipped for reverse engineering through three-dimensional positional analysis application. For a listing of capabilities available in this area please click here.
For a listing of capabilities available in this area please click here.
The Electronics Fabrication Lab (EFL) provides customized design and prototyping of electronic and mechatronic devices. Our engineersspecialize in software development and fabrication of electrical and electronics, such as instrumentation and motion control, data acquisition with system design, image/data analysis, hardware modification/upgrade, circuit design – analog/digital, printed circuit boards and root cause analysis.
For a listing of capabilities available in this area please click here.
Mechanical design engineering combines an understanding of mechanical design with materialsʼ properties and manufacturing technologies. Our expertise includes CAD, 3D modeling, additive manufacturing, flow and stress analyses, sheet metal works, motion studies, and much more.
For a listing of capabilities available in this area please click here.
SGL is Specializes in the design, fabrication and repair of all types of scientific glassware. It is equipped to work with both borosilicate and quartz glass, thus covering most requirements of research. Borosilicate glass has a high chemical resistance and excellent thermal capacity. Quartz is superior in purity having excellent optical transmittance in the UV, and can withstand temperatures up to 1,200°C.
For a listing of capabilities available in this area please click here.
For a listing of capabilities available in this area please click here.
For the data base of the machines and its location in KAUST please visit: https://corelabs.kaust.edu.sa/services/equipment
The followings summarizes the general sources of hazards:
Electric drills, pneumatic drill, underwater electric drill.
Milling machines, lath machines, CNC machines, laser cutting machines
Table saws, drop saw, dimond dicing saws, diamond saw, routers.
Potential hazard:
All the machine specifications should be studied and analyzed against the national and international standard specifications as well as the KAUST in- house standards related to: design, electricity, safety … etc The process and techniques where the machines will be used for, should be studied and analyzed for t the potential hazard and safety optimization
All the required hazard controls should be studied and applied: administrative, engineer and PPE
Safety Gloves – Safety Glasses –Face Shield - Safety Shoes incase heavy items (more than 20 kg) is handled
- - - -
Safety Glasses – Face Shield
Safety Guards
Safety Gloves – Safety Glasses –Face Shield
Machine safety guards-ventilation – dust vacuum
Safety Gloves – Safety Glasses –Face Shield
Machine safety guards/enclosure - ventilation – dust vacuum
Safety Gloves – Safety Glasses –Face Shield
Machine safety guards/enclosure- ventilation
Safety welding gloves, welding apron, auto darkening welding Helmut
Ventilation – fumes vacuum
Training is considered part of the administrative controls to reduce the potential hazardous.
The “Manufacturability Course”, available in the course catalog, is the required course for entering the workshops and handle the machines and tools.
As part of the KAUST Core Labs and Research Infrastructureʼs educational mandate, our expert staff members run training modules for our users on all equipment suitable for independent use.
As independent use broadens awareness of processes and facilitates ownership of method and data acquisition, we encourage all of our users to work independently when possible. Our staff will always be on hand to offer ongoing support and advice when needed.
Training modules, which are run bi-annually, are open to the KAUST academic community and our external users who have a service agreement with KAUST.
To be eligible for training, all applicants must first be registered on Infinity, our central booking system. For more information about Infinity, please contact clhelpdesk@kaust.edu.sa
Registration in infinity system and having active infinity account
HSE mandatory safety training.
Lab safety
Emergency and preparedness
Hazardous waste
The Prototyping and Product Development Core Lab Training inquiries: PCL.TeamLeads@kaust.edu.sa